Статор в сборе
Большинство наших заводов по производству электродвигателей производят небольшие двигатели, используя процесс внешней запрессовки.
Сердечник статора во врезанной линии после погружения и запекания, запрессованный в седло, должен обеспечивать соответствие осевого положения требованиям чертежей.
В противном случае это приведет к слишком сильному растяжению одного конца катушки, что приведет к общим трудностям сборки, а также к увеличению магнитного потенциала воздушного зазора электродвигателя, что повлияет на производительность электродвигателя.
Это также увеличит износ осевого усилия на роторе электродвигателя.
Осевое положение сердечника статора в корпусе обычно обеспечивается с помощью инструмента для запрессовки шин.

Размер герметика контролируют таким образом, чтобы положение сердечника после запрессовки соответствовало требованиям чертежа.
Чтобы гарантировать, что сердечник статора не вращается в корпусе, контакта между внутренним кругом корпуса и внешним кругом сердечника статора недостаточно, поэтому каждый электродвигатель также оснащен стопорным винтом для полной фиксации сердечника статора. ядро в корпусе.
Ротор в сборе
Сборка ротора асинхронного двигателя включает сборку сердечника ротора и вала, сборку подшипников и сборку вентилятора.
Это ключевой компонент производства электродвигателей.
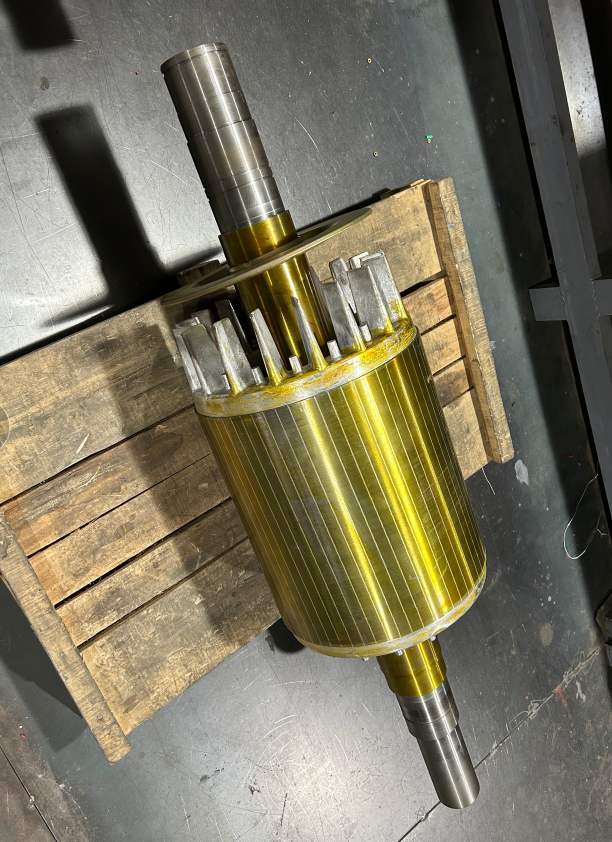
Сборка сердечника ротора и вала
При работе электродвигателя механическая мощность выводится через вал ротора, поэтому надежность соединения сердечника ротора и вала очень важна.
Если внешний диаметр ротора менее 300 мм, сердечник ротора обычно прижимается непосредственно к валу ротора; когда внешний диаметр ротора превышает 300–400 мм.
Сначала в сердечник запрессовывается кронштейн ротора, а затем в кронштейн ротора запрессовывается вал ротора.
Электродвигатели серии Y имеют конструкцию, в которой сердечник ротора большинства производителей прижимается непосредственно к валу ротора.
На производственной линии существуют три основные формы сборки между сердечником ротора и валом: посадка холодным прессованием с накаткой, посадка горячей втулкой и посадка шпоночным соединением.
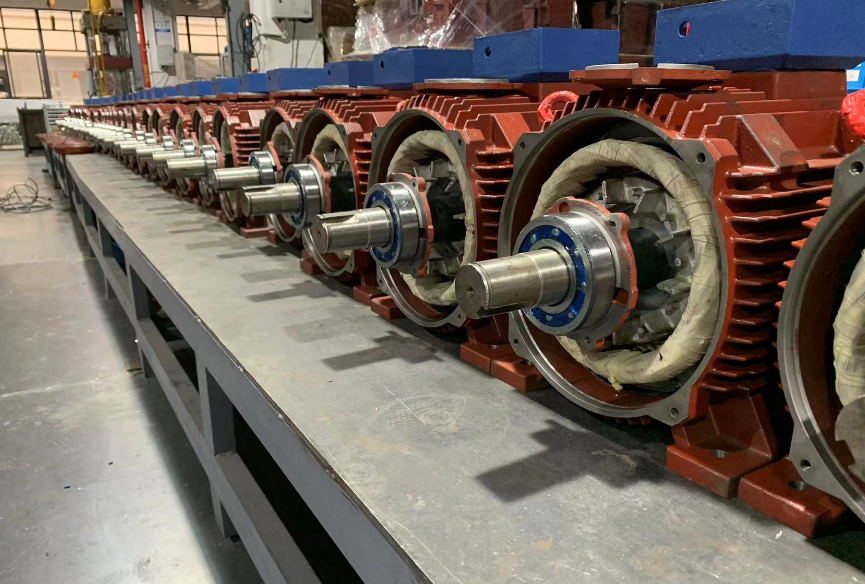
Посадка холодным прессом с накаткой. При посадке холодным прессом с накаткой процесс обработки вала состоит из: окончательной обработки напильника, накатки и шлифования, затем вдавливания в сердечник ротора, а затем окончательного шлифования удлинения вала, напильника подшипника и чистовой обработки внешнего круга сердечника. .
При использовании накатки также не допускается чрезмерный натяг.
Поскольку величина давления холодного прессования пропорциональна величине натяга, когда величина натяга слишком велика, он может не вдавливаться, либо материал может деформироваться или повредиться из-за чрезмерного внутреннего напряжения.
Горячая втулка обычно выполняется за счет использования остаточного тепла ротора из литого алюминия (или путем повторного нагрева ротора).
Процесс горячей гильзы экономит оборудование для холодного прессования, а комбинация сердечника ротора и вала более надежна.
Поскольку горячая гильза нагревается для расширения включения, а затем охлаждается, отверстие включения сжимается, удерживая включение, что обеспечивает достаточные значения натяга и высокую надежность.
Преимущество шпоночного соединения в том, что оно обеспечивает надежность соединения и облегчает организацию поточного производства.
Недостаток в том, что процесс обработки увеличивается, а шпоночный паз на валу снижает прочность вала, особенно в небольших электродвигателях.
При использовании шпоночного соединения ширина клавиши подбирается согласно заданным требованиям.
Для упрощения процесса обычно можно использовать шпоночную канавку одинаковой ширины с удлинением вала для электрических машин.
Подшипниковый узел
В асинхронных двигателях малой и средней мощности широко используется конструкция подшипников качения. Они легче подшипников скольжения, требуют менее частого обслуживания в процессе эксплуатации и потребляют меньше смазочного масла и смазки.
В то же время подшипники качения имеют небольшой радиальный зазор и больше подходят для асинхронных двигателей с малым воздушным зазором.
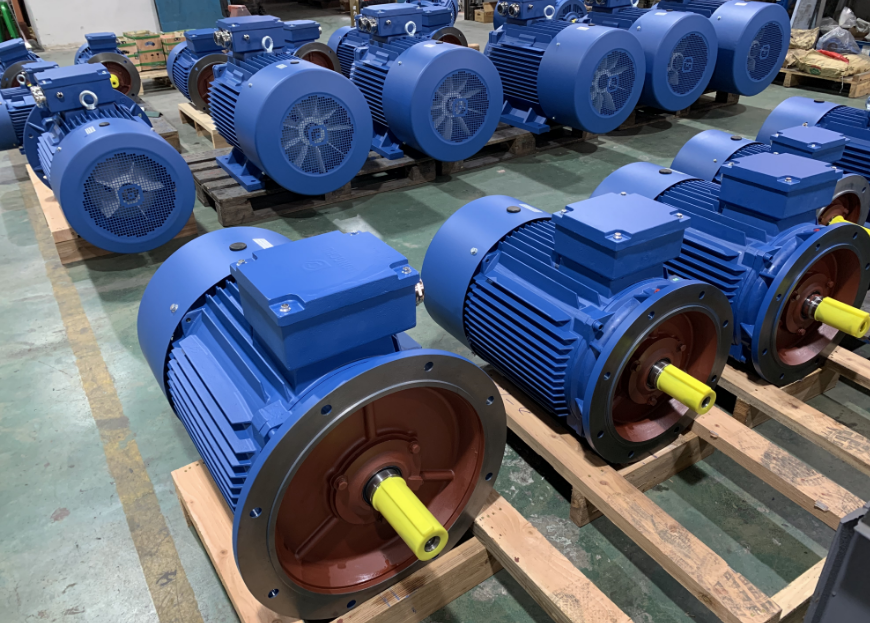
Генеральная Ассамблея
Полная сборка двигателей малой и средней мощности включает установку ротора в статор, установку других компонентов, таких как торцевые крышки, распределительные коробки, внешние вентиляторы и щеточные устройства и т. д. у многих производителей.
После полной сборки также необходимо провести испытания и внешнюю отделку мотора.
Генеральная сборка ротора в статор для производства электродвигателей
Вставка ротора в статор является одним из ключевых процессов.
Неправильная эксплуатация может легко привести к повреждению обмоток, а иногда даже к деформации вала ротора.
При установке ротора необходимо обратить внимание на соответствующее положение удлинения вала и распределительной коробки.
Если масса ротора менее 35 кг, его можно вставить в статор вручную.
Для роторов большего размера требуются подъемные инструменты.
При работе сначала поднимите инструмент за подъемное кольцо 2 и установите его на вал ротора, затем вместо этого поднимите ротор за подъемное кольцо 1 и удерживайте рычаг 3, чтобы ротор вошел в статор горизонтально и плавно.
Установка торцевой крышки
При установке торцевой крышки обычно сначала устанавливайте удлинитель, не являющийся осью.
Нанесите тонкий слой масла на поверхность упора узла, чтобы предотвратить ржавление горловины.
После установки торцевой крышки постучите вокруг торцевой крышки, чтобы затянуть торцевую поверхность торцевой крышки и седла, а затем поочередно затяните болты по диагонали.
Когда установлена вторая торцевая крышка, ротор необходимо поднять ровно (маленький мотор поднять невозможно), затем сбить упор торцевой крышки, затянуть болт.
Если две торцевые крышки установлены с разными осями или торцевые поверхности не параллельны, ротор может вращаться неподвижно, вам нужно использовать молоток, чтобы постучать по торцевым крышкам, чтобы устранить явление разных осей, а не параллельности, чтобы Ротор вращается гибко.
Затем установите внешнюю крышку подшипника, затяните винты крышки подшипника.
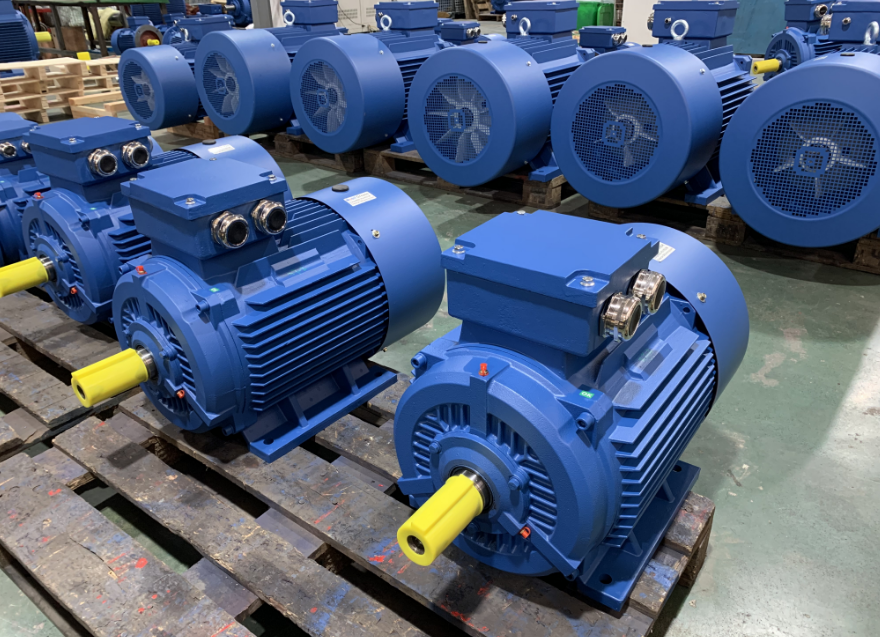
Регулировка воздушного зазора
Для подшипника качения с круглой торцевой крышкой двигателя среднего размера, когда ротор вставлен в статор, сначала должна быть установлена торцевая крышка со стороны шарикоподшипника, а затем должна быть установлена торцевая крышка со стороны роликоподшипника. предотвратить повреждение подшипника качения.
Если сначала необходимо установить торцевую крышку со стороны шарикового подшипника, винт торцевой крышки не следует затягивать. После установки торцевой крышки со стороны шарикового подшипника затяните винт.
После установки торцевой крышки отрегулируйте воздушный зазор.
Метод регулировки заключается в использовании домкрата (четыре на обоих концах) для регулировки относительного положения торцевой крышки.
Для измерения используйте линейку пробок в положении взаимной разности 120 (оба конца), до тех пор, пока однородность воздушного зазора не будет соответствовать техническим условиям стандарта.
После регулировки воздушного зазора будет установлено винтовое крепление, в горизонтальной перфорационной машине в соответствии с расположением чертежа просверливается отверстие для штифта для позиционирования клецок, и играют люди, позиционирующие штифт.
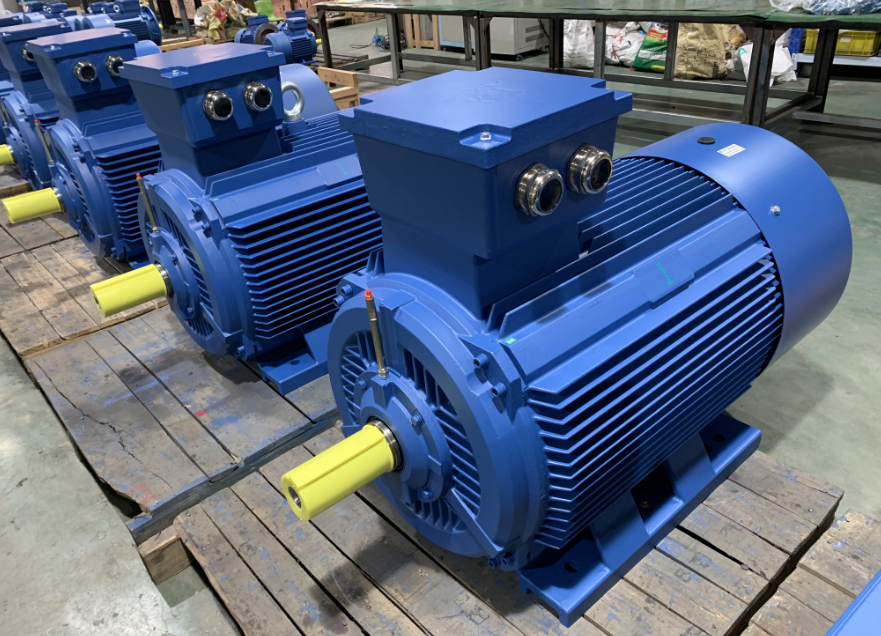
Сборка щеточной системы в силовой электронике
В электродвигателе с контактным кольцом (например, в асинхронном двигателе с обмоткой ротора большого и среднего размера).
Качество сборки щеток оказывает большое влияние на состояние проводимости; в двигателе с коллектором ситуация с коммутацией хорошая или плохая, часто тесно связанная с качеством сборки системы щеток.
Щетки коллекторного кольца и коллектора обычно представляют собой электрохимические графитовые щетки и металлографитовые щетки.
Электрохимическая графитовая щетка изготавливается из природного графита после обработки для удаления примесей и последующего спекания.
В зависимости от различного соотношения сырья его можно разделить на графитовый, коксовый и технический углерод.
Щетки на основе технического углерода имеют более высокий коэффициент сопротивления и падение контактного напряжения и подходят для двигателей со сложной коммутацией; Щетки на основе графита обычно используются в обычных двигателях.
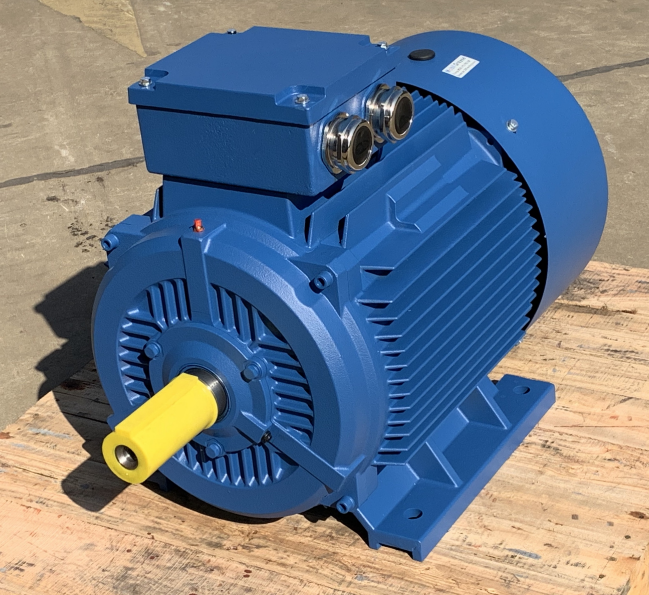
Гальванические графитовые щетки имеют меньшую твердость и более медленный износ, плотность тока обычно составляет 10-12А1см2. Металлические графитовые щетки подходят для двигателей низкого напряжения и сильного тока. Их спекают путем добавления 40–50% медного порошка в графит.
Он имеет высокую плотность, низкую твердость, низкий коэффициент износа, низкий коэффициент сопротивления, низкое падение контактного давления, медленный износ, а плотность тока обычно составляет 17-20 А/см2 для более высокого качества.
Расположение щеток в двигателе постоянного тока, поскольку в положительных и отрицательных щетках под коллектором степень износа непостоянна, поэтому необходимо разумное расположение расположения щеток.
Щетки должны располагаться на поверхности коллектора в шахматном порядке.
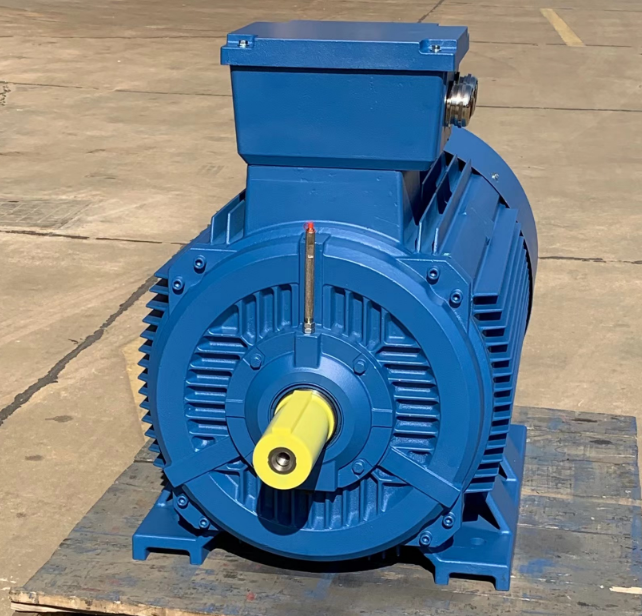
Автоматизация сборки малых двигателей электропоездов
В целях повышения производительности труда, снижения производственных затрат, сокращения цикла разработки или производства продукции, повышения конкурентоспособности продукции на рынке. Автомобильная промышленность в стране и за рубежом конкурирует за внедрение технологий автоматизации в области сборки двигателей.
Ранняя система автоматизации сборки двигателей, представленная полуавтоматической сборочной линией двигателей, использовалась для сборки небольших двигателей в больших количествах и с небольшими характеристиками.
Эта полуавтоматическая сборочная линия включает в себя автоматическое сборочное оборудование, такое как машина для загрузки ротора, машина для запрессовки подшипников, машина для запрессовки торцевой крышки и машина для затяжки винтов, функциями которых являются: загрузка статора, вставка ротора в статор, запрессовка подшипника, торцевая крышка. загрузка, бабочка и затяжка ногтей.
Основной процесс сборки выполняется машинным оборудованием, а вспомогательные работы выполняются вручную.
Оборудование этой полуавтоматической сборочной линии фиксировано и имеет определенный рабочий темп, а эффективность работы высокая, которая может достигать 25-40 с/комплект.
Для удовлетворения требований автоматической сборки многовидовой и мелкосерийной продукции в зарубежных странах разработаны гибкие сборочные ячейки (FAC) и гибкие сборочные системы (FAS), обе из которых используют роботов с компьютерным управлением в качестве основного оборудования и таким образом, имеют высокий уровень автоматизации.
Гибкая сборочная ячейка включает в себя манипулятора и несколько сборочных роботов.
Робот-манипулятор отвечает за обработку различных деталей и доставку собранных деталей на рабочую станцию сборочного робота по порядку, а затем перенос собранных деталей на конвейерную ленту для их отправки.
На сборочных роботах установлено такое оборудование, как верстаки и прессы, отвечающие за сборку различных деталей.
Гибкая сборочная ячейка позволяет собирать различные типы компонентов, а компьютерную программу также можно изменить для сборки автомобильной продукции с различными характеристиками.
На основе гибкой сборочной ячейки была доработана полностью автоматизированная гибкая сборочная система.
Эта система в основном включает в себя несколько основных частей, таких как программируемая сборочная единица, склад системы хранения и гибкая система логистической передачи, ядром которой является программируемая сборочная единица.
Программируемая сборочная единица осуществляет управление сборочным роботом путем изменения компьютерной программы и собирает различные двигатели с разными характеристиками.
Чтобы обеспечить беспрепятственную поставку комплектующих в систему сборки и выступать в качестве буфера в случае сбоя системы, гибкая система сборки имеет склад хранения.
Склад оборудован программируемыми средствами управления полками, которые позволяют компьютеру обеспечить произвольный доступ к каждой единице хранения.
Гибкая система логистической передачи состоит из конвейерной ленты или транспортного средства с автоматическим управлением (AGV), которое отвечает за обработку материалов и обмен логистикой между процессами внутри и снаружи системы.
В системах FAS обычно используется иерархическая распределенная компьютерная система управления для управления и контроля различного автоматизированного оборудования в системе.
Компьютерная система включает в себя главный компьютер, компьютер управления FAS, компьютер логистики и несколько компьютеров FAC.
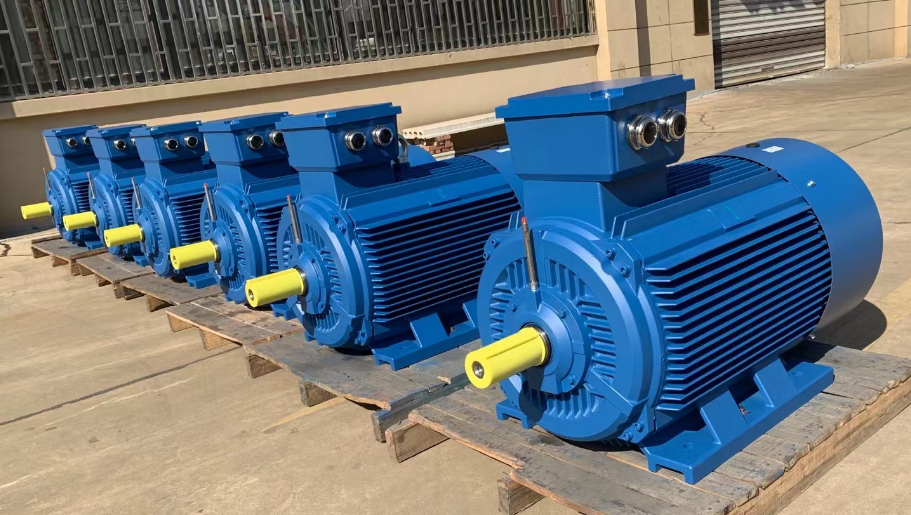
С помощью этих компьютеров система FAS может легко изменять программу и управлять системой сборки для достижения автоматической сборки двигателей различных спецификаций.
Например, разработанная за рубежом система автоматической сборки позволяет автоматически собирать 450 типов небольших двигателей с различными характеристиками.
Это показывает, что гибкая система сборки FAS не только высокоавтоматизирована, но и легко адаптируется и сегодня является направлением автоматизации сборки небольших двигателей.
Помимо автоматизации сборки, существуют также автоматические линии испытания двигателей и автоматические линии электростатической окраски.
Использование этих автоматических линий позволит значительно улучшить условия труда и повысить производительность труда, а также может создать благоприятные условия для реализации метаперсонализированного производства электромоторных заводов.
Добро пожаловать, чтобы оставить сообщение в области комментариев для любой информации об электродвигателях.
Любой запрос об электродвигателе, пожалуйста, свяжитесь с ведущим производителем электродвигателя в Китае - двигатель Dongchun следующим образом;

Dongchun Motor предлагает широкий ассортимент электродвигателей, которые используются в различных отраслях, таких как транспорт, инфраструктура и строительство.
Получите оперативный ответ.